SCM Inventory Management 1
- Lakshminarasimman V Rao
- Nov 17, 2021
- 6 min read
AMFI-SCM03-SM03-Day03-15Nov21
STUDY Notes
Agenda - Inventory, Importance of effective Inventory, cost of inventory, types, methods of classification
What is inventory management meaning?
What Is Inventory Management? Inventory management refers to the process of ordering, storing, using, and selling a company's inventory. This includes the management of raw materials, components, and finished products, as well as warehousing and processing of such items.
Inventory management helps companies identify which and how much stock to order at what time. It tracks inventory from purchase to the sale of goods. The practice identifies and responds to trends to ensure there's always enough stock to fulfill customer orders and proper warning of a shortage.
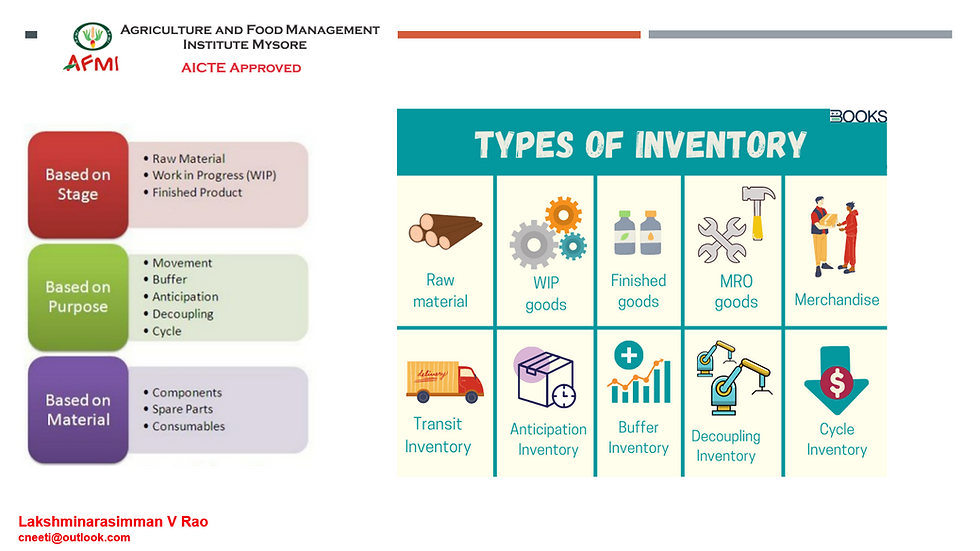

Decoupling inventory is the term used when product manufacturers set aside extra raw materials or work in progress items for all or some stages in a production line, so that a low-stock situation or breakdown at one stage doesn't slow or stop operations.
Decoupling inventory involves separating inventory within a manufacturing process so that the inventory associated with one stage of a manufacturing process does not slow down other parts of the process. In simple terms, decoupling inventory is a safety stock of sorts
MRO Inventory means maintenance, repair, and operations inventory. It includes an inventory of all items that are useful to keep a company running. Or, we can say, it includes maintaining inventories to continue manufacturing the end product.
MRO includes everything the maintenance crew does to keep your facility (and the equipment inside it) in good operating condition. In other words, the main goal of MRO is to keep your business operations running smoothly
Importance of MRO Management
Unplanned downtime in manufacturing is one of the largest causes of lost productivity, causing delays, unhappy customers and lost revenue. when there is an unexpected shutdown or failure of equipment or process. Unplanned downtime not only causes costly delays in maintenance, production schedules and order deliveries, but it also increases the chance of personnel injury, environmental incidents and emergency repairs.

Methods of Inventory Control | Materials Management
There are some selective inventory control methods to have an effective control on the inventory.
The important methods are:
1.ABC Analysis (Always Better Control)
2.VED Analysis (Vital, Essential, Desirable)
3.FSN Analysis (Fast, Slow moving and Non-moving)
4.SDE Analysis (Scarce, Difficult, Easy)
5.HML Analysis (High, Medium, Low)
6. XYZ Analysis (uncertainty)
7. Just-In-Time (JIT) Inventory System
Method # 1. ABC Analysis:
One of the widely used techniques of inventory control is the ABC (Always Better Control) analysis. This analysis is based on the annual consumption of inventory items in a year.
a. Only a small number of inventory items consume a very large share of inventory consumption during the year.
b. A little larger number of inventory items covers a moderate share of annual inventory consumption.
c. A very large number of items just cover a very small share of annual inventory consumption.
These facts gave birth to the concept of ABC analysis. The ABC approach is a means of categorizing inventory items into three classes ‘A’, ‘B’ and ‘C’.
Class A items: 10% of items have 70% of the annual inventory consumption.
Class B items: 20% of the items have 20% of annual inventory consumption.
Class C items: 70% of the items have only 10% of the annual inventory consumption.

Method # 2. V.E.D. Analysis:
This classification is applicable only for spare parts and is based on criticality. In general, criticality of a spare part can be determined from the production downtime loss, due to spare being not available when required. The VED analysis is done to determine the criticality of an item and its effect on production and other services
a. Vital (V): A spare part will be termed vital, if on account of its non-availability there will be very high loss due to production downtime and/or a very high cost will be involved if the part is procured on emergency basis.
b. Essential (E): A spare part will be considered essential if, due to its non availability, moderate loss is incurred.
c. Desirable (D): A spare part will be desirable if the production loss is not very significant due to its non-availability. Most of the parts will fall under this category. The VED analysis helps in focusing the attention of the management on vital items.
Method # 3. FSN Analysis:
FSN classification is based on frequency of issues/use. F, S and N stand for fast moving, slow moving and non-moving items. This form of classification identifies the items frequently issued; less frequently issued for use and the items which are not issued for longer period, say, 2 years.
For instance, the items can be classified as follows:
a. Fast Moving (F): Items that are frequently issued say more than once a month.
b. Slow Moving (S): Items that are issued less than once a month.
c. Non-Moving (N): Items that are not issued\used for more than 2 years.

Method # 4. SDE Analysis:
This classification is carried out based on the lead time required to procure the items.
The classification is as follows:
a. Scarce (S):
Items which are imported and those items which require more than 6 months’ lead time.
b. Difficult (D):
Items which require more than a fortnight but less than 6 months’ lead time.
c. Easily Available (E):
Items which are easily available; mostly local items, i.e. less than a fortnights’ lead time.
This classification helps in reducing the lead time required at least in case of vital items. Ultimately, this will reduce stock-out costs in case of stock-outs.
Method # 5. HML Analysis:
The cost per item (per piece) is considered for this analysis. The items of inventory should be listed in the descending order of unit value and it is up to the management to fix limits for these categories. High cost items (H), Medium Cost items (M) and Low Cost item (L) help in bringing controls over consumption at the departmental level.
This classification is as follows:
a. High Cost items (H):Items whose unit value is very high
b. Medium Cost items (M): Items whose unit value is of medium value.
c. Low Cost items (L):Items whose unit value is low.
This type of analysis helps in exercising control at the shop floor level i.e., at the use point.
Method # 6. XYZ analysis is a way to classify inventory items according to variability of their demand.
X – Very little variation: X items are characterised by steady turnover over time. Future demand can be reliably forecast.
Y – Some variation: Although demand for Y items is not steady, variability in demand can be predicted to an extent. This is usually because demand fluctuations are caused by known factors, such as seasonality, product lifecycles, competitor action or economic factors. It's more difficult to forecast demand accurately.
Z – The most variation: Demand for Z items can fluctuate strongly or occur sporadically. There is no trend or predictable causal factors, making reliable demand forecasting impossible.
Benefits-
Improves accuracy of forecasting.
Reduces stock-outs, which:
– Improves production stability and efficiency.
– Improves customer satisfaction.
Increases stock churn.
Reduces stock obsolescence.
Clarifies service levels for items with volatile demand.

Method # 7 Just-in-time, or JIT, is an inventory management method in which goods are received from suppliers only as they are needed. The main objective of this method is to reduce inventory holding costs and increase inventory turnover.is a positive cost-cutting inventory management strategy, although it can also lead to stockouts. The goal of JIT is to improve a company's return on investment by reducing non-essential costs.
JIT techniques work to level production, spreading production evenly over time to foster a smooth flow between processes. Varying the mix of products produced on a single line, sometimes referred to as "shish-kebab production", provides an effective means for producing the desired production mix in a smooth manner.
Benefits of JIT Inventory Management
Reduce Space Requirements :Companies with less inventory and improved production workflows need less room on the warehouse or production floor.Lower stock holding means a reduction in storage space which saves rent and insurance costs
Reduce Rework: Practicing continuous improvement eliminates unnecessary steps
Disadvantages
There is little room for mistakes as minimal stock is kept for re-working faulty product
companies may experience difficulty adapting to sudden surges in customer demand. Any shortage of raw materials or parts will inevitably cause delays in shipment to the customer. With time-sensitive orders, businesses risk losing customer
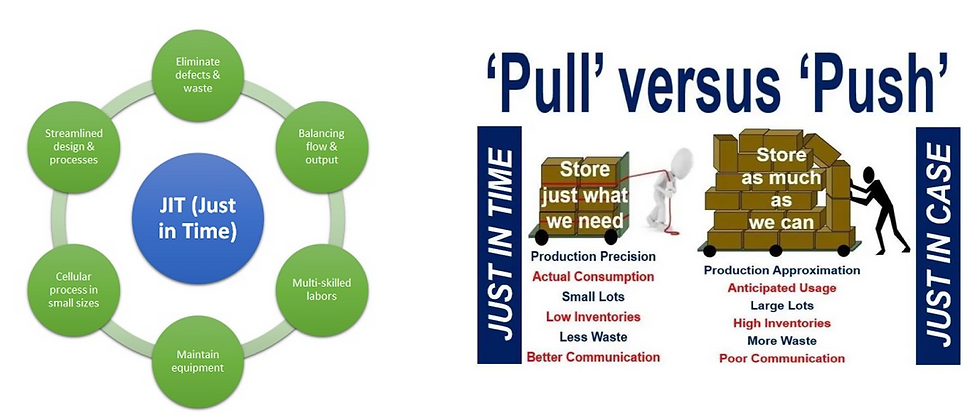
Lakshminarasimman V Rao | Supply Chain Management |Inventory Management|AFMI| Study notes | Study Material | MBA | Corporate Neeti Consulting | Mysuru
All data above is a combination of data from Internet, purpose of this doc is for research and education only and responses received from Class students and interaction.
https://g.page/corporateneeti?gm
https://fb.com/corporateneeti
Comments